Warning
This document is current with effect from the date shown on the cover page. As the International Mine Action Standards (IMAS) are subject to regular review and revision, users should consult the IMAS project website in order to verify its status at (http://www.mineactionstandards.org/, or through the UNMAS website at www.mineaction.org)
Copyright notice
This UN document is an International Mine Action Standard (IMAS) and is copyright protected by the UN. Neither this document, nor any extract from it, may be reproduced, stored or transmitted in any form, or by any means, for any other purpose without prior written permission from UNMAS, acting on behalf of the UN.
This document is not to be sold.
Director
United Nations Mine Action Service (UNMAS) 1 United Nations Plaza
New York, NY 10017
USA
Email: mineaction@un.org
Telephone: (1 212) 963 1234
Foreword
International standards for humanitarian demining programmes were first proposed by working groups at an international technical conference in Denmark, in July 1996. Criteria were prescribed for all aspects of demining, standards were recommended and a new universal definition of ‘Clearance’ was agreed. In late 1996, the principles proposed in Denmark were developed by UN- led working group and the International Standards for Humanitarian Mine Clearance Operations were developed. The first edition was issued by the UN Mine Action Service (UNMAS) in March 1997.
The scope of these original standards has since been expanded to include the other components of mine action and to reflect changes to operational procedures, practices and norms. The standards were re-developed and renamed as International Mine Action Standards (IMAS) with the first edition produced in October 2001.
The United Nations has a general responsibility for enabling and encouraging the effective management of mine action programmes, including the development and maintenance of standards. UNMAS, therefore, is the office within the United Nations responsible for the development and maintenance of IMAS. IMAS are produced with the assistance of the Geneva International Centre for Humanitarian Demining.
The work of preparing, reviewing and revising IMAS is conducted by technical committees, with the support of international, governmental and non-governmental organisations. The latest version of each standard, together with information on the work of the technical committees, can be found at www.mineactionstandards.org. Individual IMAS are reviewed at least every three years to reflect developing mine action norms and practices and to incorporate changes to international regulations and requirements.
Introduction
Animal Detection Systems (ADS) are a tool that may be used in land release processes to support technical survey (TS) and clearance. As an input to the land release process ADS require testing, in accordance with IMAS 07.12 and 07.40, to confirm that they satisfy quality requirements, particularly in terms of their capability to detect Explosive Ordnance (EO) including, landmines and other target objects that may be specified by authorities, customers and other stakeholders. While ADS is a generic term, the only animals currently in use are dogs and rats. This chapter, however, will cover Mine Detection Dogs (MDD) and Mine Detection Rats (MDR) in the context of mine clearance (including conventional ERW), while Explosive Detection Dogs (EDD) and other operational applications of ADS may be covered in the relevant annexes supporting this chapter. This chapter recognises that dogs may be used as MDD, Technical Survey Dogs (TSD) or both.
Establishing and maintaining stakeholder confidence in the reliability of ADS requires that tests of the capability and performance of ADS are rigorous, realistic, reliable and transparent. It is also important that operational tests are designed to reflect expected performance of ADS units in the field and that they are adjusted as required. Tests are carried out during initial accreditation and periodic reassessment.
Where logistically possible, tests should always be conducted in an environment replicating future intended areas for ADS operations. The nature of ADS testing is such that there may be some aspects of the situation that do not exactly replicate operational circumstances and conditions. Nevertheless, testing authorities and agencies shall strive to create test conditions that give mine action actors confidence that a successful test result ensures minimum required operational capability and technical competence to conduct safe ‘live’ land release operations under field conditions.
Constraints of time, cost and efficiency, as well as prevailing security situation, may mean that daily operational testing at task sites in support of day-to-day operations cannot satisfy all the requirements of this IMAS, but any such testing should still seek to satisfy similar criteria, so far as possible, to ensure that tests are valid in relation to live operations.
The accreditation process of ADS operators is divided into two (2) steps,
- Organisational accreditation and
- Operational accreditation.
Organisational accreditation is a formal method of assessing an organisation against a set of pre- determined criteria and is not related to any specific operation, but instead focuses on a general assessment of an organisations’ operational and technical capabilities and internal quality management processes. Organisational accreditation ensures the organisations technical and operational capability to deliver ADS service to set IMAS.
Operational accreditation is a formal method of assessing that individual ADS units operationally deployed by an accredited ADS organisation meet required operational criteria.
To obtain organisational accreditation, an ADS organisation shall pass a two-stage review process conducted by an ADS Accreditation Board appointed by the National Mine Action Authority (NMAA) / National Mine Action Centre (NMAC):
- Stage 1 – Documentation review; The ADS organisation shall be assessed on its organisational, administrative and technical capabilities.
- Stage 2 – Physical review; The ADS organisation shall be assessed at their training facility in the country of operations, where operational capability shall be evaluated, based on the ability of a sample ADS units.
Stakeholder confidence is further maintained through on-going monitoring conducted by NMAA/NMAC and analysis of ADS performance data collected during operations on LR sites. Testing and monitoring go hand in hand to ensure that operators, authorities and other stakeholders trust ADS units to perform the tasks that they are assigned to the required standards.
1. Scope
This standard sets out requirements and guidelines for the external accreditation and operational testing of Animal Detection Systems (ADS).
This standard does not apply to the Internal Quality Management (IQM) processes of ADS organisations that are granted organisational accreditation such as e.g. daily pre-work testing of ADS units. ADS organisations should apply IQM procedures outlined in assessed documentation for internal testing.
2. References
A list of normative references is given in Annex A. Normative references are important documents to which reference is made in this standard and which form part of the provisions of this standard.
3. Terms, definitions and abbreviations
A complete glossary of all the terms, definitions and abbreviations used in the International Mine Action Standards (IMAS) series is given in IMAS 04.10.
In the IMAS series, the words 'shall', 'should' and ‘may’ are used to indicate the intended degree of compliance.
-
'shall' is used to indicate requirements, methods or specifications which are to be applied in order to conform to the standard;
-
'should' is used to indicate the preferred requirements, methods or specifications; and
-
'may' is used to indicate a possible method or course of action.
The term 'National Mine Action Authority' (NMAA) refers to the government entity, often an interministerial committee, in an EO-affected country charged with the responsibility for broad strategic, policy and regulatory decisions related to mine action.
Note: In the absence of an NMAA, it may be necessary and appropriate for the UN, or some other body, to assume some or all of the responsibilities of an NMAA.
The term ‘Accreditation’ refers to the process by which an ADS organisation is formally recognized as competent and able to plan, manage and operationally conduct animal detection activities safely, effectively and efficiently.
The term ‘Animal Detection System` (ADS) refers to the combination of animals, handlers, supervisors, managers, equipment, facilities, policies, procedures and other associated functions, that interact to provide a tool intended to detect vapour from Explosive Ordnance (EO). ‘Vapour’ may include vapour from the case material and other substances as well as from explosives.
The term 'ADS Organisation' refers to any organisation (government, NGO or commercial entity) responsible for implementing mine action projects or tasks with the use of ADS.
The term ‘ADS Unit’ refers to an animal and its handler (under the direction and monitoring of team/site management).
The term ‘Demining’ refers to activities that lead to the removal of EO.
The term ‘Explosive Ordnance’ (EO) is interpreted as encompassing mine action’s response to the following munitions:
- Mines
- Cluster Munitions
- Unexploded Ordnance
- Abandoned Ordnance
- Booby traps
- Other devices (as defined by CCW APII)
- Improvised Explosive Devices
The term ‘Mine Detection Dog’ (MDD) refers to a dog specifically trained to detect and correctly indicate vapour from EO, normally in the minefield environment/setting.
The term ‘Explosive Detection Dog’ (EDD) refers to a dog specifically trained to locate and correctly indicate the presence of defined explosive substances or other relevant target objects.
The term ‘Mine Detection Rat’ (MDR) refers to a rat specifically trained to detect and indicate vapour from EO, normally in the minefield environment/setting.
The term ‘Target Object’ is used to describe a specified object that ADS units are required to detect during search and clearance operations.
The term ‘Test Item’ is used for EO that are laid in the test site for detection by the ADS unit. The term 'Target Odour' is used to describe the scent from the target object or the test item.
4. Aim of organisational accreditation
The aim of the organisational accreditation is to provide confidence in the ability of demining organisations to, repeatedly, train, deploy, operationally manage and sustain quality of ADS units in operational deployments during land release operations.
4.1 Stage 1 - Documentation review
To obtain organisational accreditation ADS organisations shall demonstrate that they possess the requisite technical and physical requirements for ADS training, provide relevant training manuals for training of ADS units, present implemented Standard Operating Procedures (SOPs) covering operational procedures and IQM Systems, kennelling and animal welfare procedures.
An ADS Evaluation Board will review and evaluate the documentation provided by the ADS organisation based on requirements outlined in National Mine Action Standards (NMAS) or National Technical Specifications and Guidelines (NTSG).
The ADS Evaluation Board will provide a recommendation to the NMAA/National Mine Action Centre (NMAC) on whether the submitting organisation meets these requirements.
If an ADS organisation fails to obtain organisational accreditation from the NMAA/ NMAC to progress to the physical review, the ADS organisation will be eligible to re-apply if/when identified shortcomings are rectified.
ADS organisations will not be awarded organisational accreditation status if it is determined that they have falsified data and records in any of the forms, statements or attachments that they have submitted, or if they try to interfere with any monitoring or inspections, as outlined in IMAS 07.30.
4.2 Stage 2 - Physical review
The physical review should occur as soon as practically possible after the documentation review has been finalised. The timing of the physical review will be determined in consultation with the ADS organisation.
The physical review should be conducted and evaluated according to procedures and criteria outlined in the documentation approved during the document review. Building on the results of the documentation review, the ADS Evaluation Board assesses whether the ADS organisation is recommended for organisational accreditation based on the combined result of the two reviews.
5. Aim of ADS operational accreditation
During operational accreditation ADS organisations are assessed using operational tests. The aim of the operational accreditation is to provide confidence in the ability of individual ADS units, to detect all presented target objects with a defined and stipulated minimum of false indications, following accredited operational procedures during land release operations. Currently, ADS are used for Clearance, Technical Survey (TS) and for Quality Control as a part of the wider Quality Management System (QMS). This chapter recognises that there may be other applications of ADS, which fall outside of the scope of this IMAS. ADS units shall only be deployed to conduct LR tasks in line with operational procedures for which they have been accredited
To achieve this, the testing procedures shall:
- be appropriate to the capabilities and capacities of the test agency or authority;
- be subject to quality management by the testing agency or authority in accordance with IMAS 07.12;
- replicate operational circumstances and conditions, so far as is reasonably practicable; correspond to the procedures and methodologies that the ADS unit will use during land release operations;
- not offer the ADS unit unintended clues as to the whereabouts of test items; in other words, not be predicted, guessed or otherwise ‘manipulated’ by the handler;
- be adjusted in light of the results of analysis of performance data relating to the test process;
- be ideally adjusted in light of the results of analysis of data relating to the operational performance of ADS units that have undergone testing on the test area not less than 400m2;
- be kept confidential when they relate to the number and location of test pieces in test areas; and
- be in accordance with the ADS organisation`s accredited SOPs.
5.1 Requirements for operational testing
5.1.1 Planning
Prior to selecting the location of the test facility and establishing the test areas the authority or agency responsible for testing of ADS units should conduct a survey of the proposed site, to confirm that it will offer sufficient space, environmental conditions, access and other features necessary to satisfy the requirements of this standard. The initial survey should additionally investigate:
-
applicable legislation and legal requirements;
-
current use of the land, including by animals;
-
evidence of existing EO or explosive contamination;
-
whether the land has previously been subject to EO clearance and/or in-situ open burning or demolition;
-
security issues and any need for fencing/guarding;
-
land ownership/leasing arrangements;
-
landscape, fluctuations, vegetation and soil, including drainage and susceptibility to flooding;
-
direction and strength of prevailing winds;
-
weather and its potential impact on soil and the ability to operate ADS units;
-
altitude and temperature difference to intended operational areas (requirement for acclimatisation);
-
evidence of pollution by petroleum products, fertilisers, chemicals, garbage and metals (including bullets and shrapnel);
-
the likelihood and prevalence of atmospheric pollution from road traffic, industry or domestic burning; and
-
the separation of the site, and the ability to shield it from disturbances.
When planning the test site planners should take into account:
-
the anticipated throughput of ADS units requiring testing;
-
any seasonal limits or influences on operations/testing;
-
access to sufficient amount of test items;
-
avoidance of excessive noise, pollution or other disturbance from outside the site;
-
the level of concurrent testing required to satisfy programme needs;
-
the need to allow a rest time between each use of individual test areas;
-
accredited procedures/methods used by ADS organisations and their implications for the shape, size and arrangement of boxes/panels/search area and the need for access areas around/between boxes/panels/search area;
-
climate, altitude, the availability of terrain, soil and vegetation conditions representative of those found at operational work sites;
-
any need for training areas sufficiently remote from test areas to satisfy the requirements of this standard;
-
any anticipated requirement to test ADS units in the TS role in unprepared, vegetated area with unknown disturbances;
-
any anticipated requirement to test ADS units in mechanically processed land;
-
the need to manage the site safely and efficiently;
-
the ease of access to resources such as water and power and for visitors to the site;
-
security aspects; and
-
costs of establishing, running and maintaining the test site.
The test site establishment plan should be documented and approved by the national authority or other competent body.
6. Establishing and maintaining the test site
6.1 Establishing test areas
Sufficient test areas should be established to meet testing requirements. A commonly used procedure, that may be used, is to lay out the test site in 10m x 10m boxes with safe lanes in between. These boxes may be grouped into panels. Boxes in this format:
-
are commonly used operationally;
-
are easy to establish, monitor and control; and
-
will allow searches from different directions making the test less reliant on a favourable winddirection. Panels created of grouped boxes can be searched in a similar way.
The test facility may also be established without using the traditional 10x10 meter boxes with test items placed and measured between clearly marked and permanent “fix-points” surrounding the area. An advantage of not using the traditional boxes is that the test manager is afforded greater flexibility to arrange test areas according to the ADS organisation`s specific requirements, e.g. boxes, panels, road clearance, vegetation etc and it also provides the possibility to arrange “empty” test areas that cannot be “known” by the ADS units undergoing assessment. Another advantage of such a design of test facility is that it minimises the required total area for the test site as the flexibility of “layout” reduces need for access lanes as well as rest time between tests.
6.2 Required number of test items
There should be a minimum of three test items within the overall test area and zero or one test item in each of the 10x10m boxes or panels. At least one box or panel should have zero test items, meaning that that 75% of the boxes or panels in a test area should have test items while 25% should be free from test items.
6.3 Maximum number of false indications
A maximum of three false indications are accepted during a single operational test of an individual ADS unit. If an ADS unit has more than three false indications before the test is completed, the test will be terminated, and the ADS unit has failed the test.
6.4 Action on indication and false indication
The following definitions and principles shall apply:
-
an ‘Indication’ is the spot pointed out by the handler as the animal indication point. It is usually located in front of the animal.
-
a ‘Miss’ is when the animal has searched the full area around a test item where an indication would have been correct and has not indicated within 1.25 meters from the centre of the test item.
-
a ‘False Indication’ in an empty box/panel1 is any indication in that box/panel.
-
a ‘False Indication’ in a box/panel with a test item is any indication that is more than 1.25 meters away from the centre of the test item.
-
if an ADS unit passes a test item in a lane without indicating, the search shall continue until the point where the ADS unit passes the test item in the next search lane. In the next search lane, if there is still no indication within the 1.25m from the centre of the test item, the ADS unit has missed the test item and the test shall be terminated (as illustrated in the figure below).
-
a ‘Correct Indication’ in a box/panel with a test item is an indication within 1.25 meters of the centre of the test item. Following a correct indication search of the box/panel is terminated.
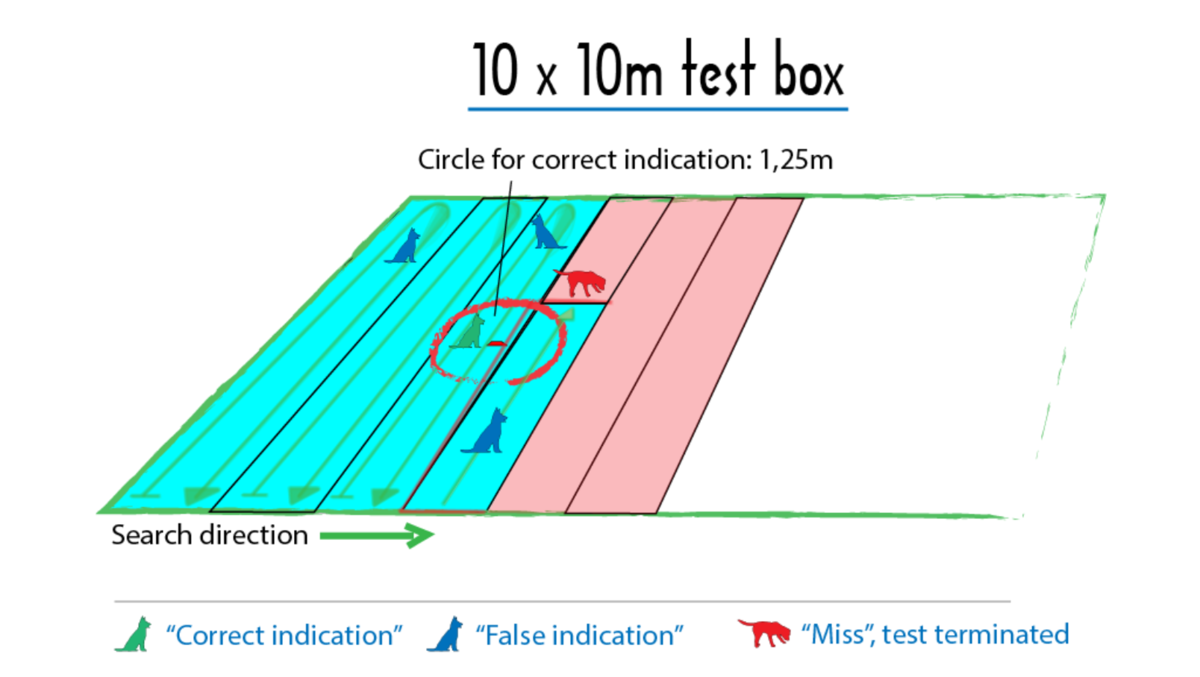
If an animal indicates a test item in a box or panel, further search in that box shall be ceased and a new box shall be allocated to complete the test. New boxes or panels shall be allocated to a point where:
-
the ADS unit has missed a test item;
-
the ADS unit has given 4 false indications; or
-
the ADS unit has indicated 3 test items correctly without missing any test item and with 3 or fewer false indications.
6.5 Required size of test area
Each ADS unit is required to find three test items during an operational test in order to pass. The required test area per ADS unit will vary depending on the number of false indications, from a minimum of 500m2 to a maximum of 800m2 per ADS unit.
Any box or panel with no test items in it may be re-used immediately.
Boxes or panels that contain test items, and where a correct indication has been made during an operational test, may not be re-used for another test for a minimum of fourteen days.
One ADS unit should be tested in a minimum of 5 boxes or panels to a maximum of 8 boxes or panels.
Test boxes and panels with no test items may be re-used immediately, as well as those boxes/panels with test items but where an ADS unit made a false indication. As a result some of the boxes/panels within a testing area may be available for use by more than one ADS unit within a two week period, as such, the actual number of test boxes/panels that need to be set aside when conducting operational tests on multiple ADS units will not necessarily equate to eight boxes per ADS unit. On average the area required is 400 m2 per ADS unit tested. ,Below are some examples:
ADS tested within a 2 weeks period | Number of test boxes/panels required |
---|---|
1 | 8 |
2 | 8 |
4 | 16 |
10 | 40 |
20 | 80 |
Additional test boxes or panels may be required for training purposes.
Test areas shall:
-
be separated from adjacent test areas, and areas required for administrative purposes by a distance sufficient to allow ADS units to move freely around the perimeter of the box/area/search area;
-
be sufficient in size to ensure all ADS units, subject to testing, are provided with a relevant search area, outlined for each specified method/procedure;
-
be marked and recorded, using a fixed, clearly visible benchmark, with a metal recognition pole (at least 30cm long) driven into the soil at each corner of each test area perimeter until its top is at surface level (unless the test area will be subject to mechanical processing, when a similarly accurate offset marking system should be adopted to allow processing of the entire test area);
-
be mapped showing the positions of turning/perimeter points, relative to each other and to the fixed benchmark location, to an accuracy of within +/- 5cm;
-
be away from steep slopes (irrespective of whether such terrain may be encountered during operations) to avoid the risk of test items moving should slopes slump or slip;
-
correspond to the procedural method (or methods) that the ADS units will apply during field operations, including boxes, lanes or other arrangements adopted during field operations. If multiple methods will be applied then multiple test areas should be established, each corresponding to an applicable layout, methodology or procedure;
-
include soil, vegetation and terrain characteristics comparable to those encountered at operational sites;
-
include access to data from a weather station or other source capable of providing continuous readings before and during testing;
-
be free from undesired explosive or other contaminants;
-
be large enough to allow concurrent testing and re-testing of ADS units adequate for the scheduled and contingency accreditation testing and reassessment needs of the mine action programme;
-
allow for searches from different directions in response to changes in wind direction; and
-
include enough space for the establishment of training/practice areas far enough away from the test areas to avoid any cross-contamination or other effects that may invalidate test results.
The boundaries of test boxes/panels/search areas should be marked using the same materials and procedures as are encountered on operational sites. If test authorities decide that visible marking should not be present on the test site, then suitable measures should be taken to ensure that the perimeter of test areas can be identified using below ground level metal pickets or other readily discoverable methods.
6.5.1 Re-use of boxes
Following a correct indication on a test item, the minimum required rest time before the box/panel can be re-used for another ADS unit is two weeks. The time may be reduced to a period of no less than one week if the site experiences weather conditions, including periods of heavy rain and sunshine or water sprinkling during that time.
A box or panel where an ADS unit has given a false indication may be re-used to test another ADS unit, with no minimum rest time between use.
6.6 Test site security
Adequate security shall be established, maintained and monitored at the site to ensure that the validity of test areas is preserved and to satisfy normal personnel and property safety and security requirements.
If the test site has been subject to unauthorised intrusion, the site shall be thoroughly checked to ensure that it remains suitable for ADS units` testing. Any aspects found to have been compromised in any way shall be corrected before restarting testing.
6.7 Vegetation cutting
Vegetation cutting on ADS test sites should be carried out using equipment and methods that will not disturb the ground and leave undesired scent traces from humans and tools on the ground. The same minimum time delay between vegetation cutting and survey/clearance used on operations should be applied between vegetation cutting and testing on a test site.
6.8 Selection, storage, handling and use of test items and recognition pieces
All test items and recognition pieces should be located at least once a year using a metal detector, preferably after the period with the heaviest rain or snowfall. The locations should then be compared with records to ensure that no migration has occurred, and that no foreign items have been introduced to the test box.
6.8.1 Selection
Test items shall be representative of target objects (mines, ERW, cluster munitions remnants, IEDs) that will be encountered during operations. EO recovered during field clearance operations should be used as test items wherever possible. EO obtained from stockpiles or stores may be used as test items as an alternative.
6.8.2 Storage
Test items recovered during field operations should be stored separately from test items obtained from stockpiles/stores.
Test items should not be stored in close proximity to paints, petroleum products, fertilisers and chemicals prior to use.
6.8.3 Handling
Disposable gloves (preferably nitrile gloves or similar) should be worn at all times when handling test items. New gloves should be used for each new test item to prevent cross contamination.
All test items, tools, accessories and recognition pieces shall be decontaminated prior to their use in a test area, using the available and approved method for achieving this.
All test items and recognition pieces must be stored, preventing contamination and cross- contamination to occur.
6.8.4 Placing test items in test areas
The location of each test item within a test area shall be irregular and unpredictable. The minimum distance between any two test items shall be 3 meters.
Test items shall be buried at different depths representing the range of depths encountered under operational conditions, as indicated by evidence from operational monitoring/information management systems and in accordance with required maximum clearance depth specified in NMAS/NTSG. At least one test item should be surface placed and accessible for the ADS unit during search to ensure correct indication behaviour for such test items.
During testing of an ADS unit for TS, no point in a test panel that contains no test items should be within 10m of any test item in an adjacent lane or other area. This is to avoid the animal responding towards test items in adjacent panels.
The location of all test items in a box, panel or search area shall be recorded to an accuracy within +/- 20mm and shall be recorded on the test facility map.
When burying test items:
-
disposable gloves (preferably nitrile gloves or similar) or double plastic bags should cover the hands during any contact with the soil. If the hand protection splits during excavation, it should be immediately replaced;
-
soil disturbance should be minimised. The top plug of soil should be kept in one piece if possible;
-
surplus soil due to the added volume of the test item should be removed to outside the test site, and not spread inside the box or neighbouring boxes;
-
the original soil should be used to fill around the test item. The top plug should be re- placed on top of the test item; and
-
only decontaminated equipment should be used during the test site preparation and during handling of the test items.
6.8.5 Use of recognition pieces
When low or zero metal content test items are used, the test site management shall ensure that recognition pieces are placed to allow confirmation of the location of test items with metal detectors, without the need to disturb the ground. Recognition pieces should be placed in a way to allow and facilitate accurate positioning of the centre of a test item.
The recognition pieces in use at a test site shall:
-
all be made of the same material (such as cut reinforcing bar);
-
not individually exceed 15g weight;
-
be decontaminated as if they were test pieces;
-
be placed in the ground centrally under the test item; and
- be placed taking precautions to preserve the decontaminated status of the test piece and recognition piece.
Whenever recognition pieces are used in conjunction with one or more test items in a test area, at least two additional recognition pieces shall be placed in the test area at locations away from test items to confirm that ADS units are detecting the test item rather than the recognition pieces.
6.9 Soak times after establishment of the test site
The required soak time depends on the moisture in the soil and ground/air temperatures, which facilitates natural transportation of the target odour from the test item to the surface. An ADS test site should have a minimum soak time of three months before use (although six months is recommended if practicable), in order to permit:
-
the target odour to migrate to the soil surface, contaminate the topsoil, and start to evaporate into the air; and
-
any ground disturbance resulting from the burial of the test items to diminish.
In areas with little or no rain, the test site should be watered several times during the soak period. In areas with cold winters, the test items should be allowed to rest in the ground over the winter.
The same soak time is required for all test items, whether buried, partially buried or fully exposed. No buried test item should be moved or disturbed during the soak period.
7. Management of testing
All ADS operational tests shall be overseen by a competent and authorised test manager. Individual tests may be monitored by competent and authorised test monitors satisfying the monitoring competence requirements detailed in IMAS 07.40.
7.1 Provision of training areas
ADS organisations may wish to train and acclimatise their ADS units in a similar environment to the test site. In this case, the test manager shall ensure that the ADS organisation is provided with a sufficiently large training area outside the immediate operational test area, established and prepared in the same way as the test areas, and containing test items of the same type. The test monitor shall provide the ADS organisation with details of training items and their coordinates.
Training shall not occur at any time in areas reserved for testing.
7.2 Minimum test requirements
Time taken for an ADS unit to search a specific test box/panel should be recorded and may be used to extrapolate expected daily productivity during the operations. Assessed ADS units shall adhere to:
- the normal working procedures and practices of the ADS organisation; and
- the prevailing circumstances and conditions.
The aim of the operational test is to provide confidence in the ability of an individual ADS unit, to detect specified target objects with a defined minimum of false indications, during land release operations. ADS units testing should adopt as minimum accuracy criteria:
- in a clearance role, ADS unit’s indications should be within 1 meter, measured from the centre of the test item; In circumstances where it is clear that the ADS unit is indicating, an absolute maximum buffer of 0.25 meter shall be allowed in addition to the 1m limit; and
-
when testing an ADS unit for TS application, an appropriate maximum performance indication distances should be defined by the NMAA.
-
the prevailing circumstances and conditions.
The aim of the operational test is to provide confidence in the ability of an individual ADS unit, to detect specified target objects with a defined minimum of false indications, during land release operations. ADS units testing should adopt as minimum accuracy criteria:
-
in a clearance role, ADS unit’s indications should be within 1 meter, measured from the centre of the test item; In circumstances where it is clear that the ADS unit is indicating, an absolute maximum buffer of 0.25 meter shall be allowed in addition to the 1m limit; and
-
when testing an ADS unit for TS application, an appropriate maximum performance indication distances should be defined by the NMAA.
7.3 Actions before testing
Prior to testing, the ADS organisation shall notify the test manager of any variations from the ADS organisations` SOPs necessary to meet test requirements. Any such variations shall be limited to the minimum necessary and should be agreed with the relevant accrediting body.
The test manager shall:
- review all relevant aspects of the SOPs of the ADS organisation being tested, and clarify any areas of uncertainty;
-
confirm that the intended test site is clear of any time restrictions relating to its previous use for testing;
-
inspect the test site to ensure that it is properly prepared and ready for use;
-
agree with the ADS organisation that any proposed observers may observe the test;
-
provide a test briefing, to all test participants and any observers, covering as a minimum: Site working practices, procedures and safety precautions;
-
site layout including administrative, test, rest and observation areas;
-
restrictions on the movement of personnel during testing;
-
strict requirement that observers do not disturb or influence the conduct of the test; and
-
agree with the ADS organisation that weather and site conditions are satisfactory, in accordance with the ADS organisation’s SOPs, for the test to proceed, and jointly document that agreement.
7.4 Conduct of testing
The test manager shall assign test areas to the ADS handler immediately prior to the operational test. The ADS handler shall have the right to inspect the test areas prior to the test, provided that the test areas are not physically entered or disturbed during the inspection.
Tests shall be monitored by the test manager or other competent and authorised test monitor. Monitoring of the tests shall be carried out so as to minimise distraction or disturbance of the animal during testing.
The test manager shall monitor testing and implement effective measures, such as the required rest time, search intervals to ensure that no animal indicates at a location in response to a previous indication by another animal at the same location.
The ADS handler may evaluate the wind direction and other environmental factors prior to the test in accordance with the ADS organisation’s SOPs and decide the search direction. The ADS handler may change the search direction at any time.
The ADS handler may request to terminate the test if at any time they believe that the animal is suffering from a lapse in concentration or for some reason is not working properly. The ADS handler should be permitted to request a termination of the test for one animal, and conduct a new test with a different animal, provided that the second animal can perform the complete test.
The test manager may terminate the test:
-
when planned test activities are complete;
-
for safety reasons;
-
at the request of the ADS handler; and/or
-
whenever there is any reason to doubt the continued validity of the test.
A single termination of the test may not constitute a failure to pass the test and the ADS organisation may ask for a new test for that ADS unit at any time. Repeated terminations of testing of an animal or ADS unit may be grounds to refuse/withdraw accreditation and should be subject to assessment by the test manager to determine appropriate action to re-test the ADS unit or recommend other action.
Photos and videos of the test may be permitted by the test manager for monitoring and training purposes, provided that they do not interfere with the conduct of the test, nor make available information to ADS organisations that might compromise the validity of future tests.
7.5 Results of testing
The following pass/fail criteria should be applied:
-
the ADS unit shall indicate all test items in a test area;
-
the ADS unit shall provide no more than 3 false indications during the entire test;
-
the ADS unit should comply with the demining organisation’s SOPs (including any variations previously agreed to satisfy test requirements); and
-
scratching or physically actively manipulating the surface or the test item during an indication is a fail criterion for MDD, while this behaviour is permitted for the much lighter MDR.
The test manager may additionally provide ‘observations’, as defined in IMAS 07.40, to the ADS organisation. Observations do not constitute a test fail or quality nonconformity in themselves but may highlight aspects of performance during the test that may benefit from review by the demining organisation and possible improvement action.
7.6 Acknowledgement of test results
The documented record of test results should include the signature of the ADS handler, as well as the test manager or monitor, any comments on the results of the test, including acceptance of the results or any appeal against the results lodged by the ADS organisation.
7.7 Right of appeal
On completion of the test, the ADS organisation should have the right to appeal a test result if it believes that an indication assessed to be false was in fact correct. The test manager, or authorised monitor, should inspect the site and compare the location of the animal’s indications with the recorded locations of test items and the documented pass criteria. Any indication assessed on appeal to be correct rather than false shall be disregarded from the test results.
The NMAA should ensure that a higher authority is identified and available for further recourse in the event that an ADS organisation does not accept the result of an appeal and wishes to elevate the matter.
7.8 Follow up action
Following a pass result, the test manager should confirm to the demining organisation the date by which the next test of the ADS unit must have been completed to satisfy accreditation requirements.
A ‘fail’ result should be treated as a nonconformity and managed in accordance with the requirements of IMAS 07.12 and 07.40. Root cause analysis (RCA) should be carried out, considering all aspects of the animal/handler relationship and the influence of other parts of the demining organisation’s systems and procedures, to identify any necessary corrective and improvement actions required on the part of the demining organisation.
Agreed actions, and readiness to submit an ADS unit, individual handler, or animal for retesting, should take into account the different natures of the relationships between handler and animal depending upon the species of animal. In particular dogs should have a unique relationship with a handler, and be tested in that combination, whereas rats may be tested in combination with any handler
Re-testing of the ADS unit, individual handler or animal should only take place once the ADS organisation has implemented and confirmed the effectiveness of agreed corrective and improvement actions.
7.9 Records
7.9.1 Records of the test site
Records of the test site shall include, as a minimum:
-
a map of the test site showing prominent topographic features, the boundaries of the test site, test box numbers if applicable, boundaries of the test boxes if applicable, benchmarks, administration areas and relevant supplementary information such as the prevailing wind direction;
-
a map of each test box showing the test box or lane number; the exact location of the test box/lane markers; reference to bench marks; the location of the test items; the depth, type, and state of each test item; any recognition pieces located under the test items and elsewhere in the boxes; details of the people responsible for the preparation of the box; and the date when the box was prepared;
-
details of the initial soak time period following initial preparation of test areas;
-
a schedule of testing including rest times following each use of test boxes/panels;
-
results of test area inspections to confirm suitability and readiness for testing; and
-
results of internal and external monitoring of the test site, in accordance with IMAS 07.40.
7.9.2 Records of testing
Records of testing shall include, as a minimum:
-
the date and time of testing;
-
the ADS organisation subject to test;
-
the name and/or unique identifying reference of handlers and animals subject to testing;
-
identification of the test area associated with each animal and/or handler;
-
weather conditions and other relevant environmental factors during the test;
-
the results of the test;
-
signatures of test manager/monitor and handler;
-
any appeals and the results of those appeals; and
-
credentials of test managers and monitors;
Additionally, for internal use only by the test site management, the location of all indications, true and false, made by the animal during the test.
7.9.3 Security of records
Records identifying the location and number of test pieces within test areas shall be kept securely and shall only be made available to those members of the test site management who need to know the information. Individuals who have access to records detailing test piece locations and numbers should have no affiliation to any ADS organisation that will be tested at the site.
7.10 Monitoring and improvement of testing
All activities at the test site shall be subject to monitoring in accordance with IMAS 07.40.
Authorities and test site management shall implement effective measures to ensure that opportunities for improvement are identified, assessed and, where appropriate, acted upon.
8. Responsibilities
8.1 National Mine Action Authority
The NMAA, or an organisation acting on its behalf, shall:
-
establish systems, procedures and facilities for the operational testing of ADS operating within the demining programme in accordance with the specifications and guidelines included in this standard;
-
provide ADS organisations with test items for training and provide training area within the accreditation area;
-
accredit and appoint an ADS operational testing authority, to include a suitably qualified and experienced test manager, to manage ADS operational testing on behalf of the NMAA in accordance with the procedures established by the NMAA and relevant national standards;
-
produce standard working procedures for the operational test site;
-
identify an individual or organisation responsible for dealing with appeals from ADS organisations; and
-
monitor the work of the ADS operational test authority, ensure that the operational testing system is being applied in a fair and equitable manner, and that planning has taken place to ensure that the requirements for operational tests do not interrupt or delay land release operations.
The NMAA, or an organisation acting on its behalf, should conduct periodic external QA audits on the ADS operational testing authority.
8.2 Test site management
The test site management shall:
- prepare the test site in accordance with the requirements set out in this standard;
- manage testing of ADS units objectively and impartially, and in accordance with the requirements set out in this standard;
- promptly provide results of tests to ADS organisations;
- maintain records of the test site and of testing;
- maintain adequate and appropriate security of test site data;
- make test results and the analysis of those results available to other stakeholders as directed by the NMAA;
- implement an effective internal quality management system; and
- comply with the requirements for external quality monitoring as directed by the NMAA.
8.3 ADS organisation
The ADS organisation shall:
-
establish SOPs for the use of ADS in land release operations that are consistent with relevant national standards, or in the absence of national standards, with IMAS;
-
make a copy of the ADS organisation’s SOPs available to the test manager;
-
agree any variations to SOPs, necessary to satisfy test requirements, with the test manager and accrediting authority;
-
assist any appointed ADS operational testing authority with the establishment of systems, procedures and facilities for the management of ADS operational testing; and
-
cooperate with the appointed ADS operational testing authority in the management and maintenance of national ADS test sites.
In the absence of a NMAA, the ADS organisation should assume additional responsibilities. These include, but are not restricted to:
-
assisting the host nation, during the establishment of a NMAA, in the development of systems, procedures and facilities for the operational testing of ADS; and
-
in cooperation with other ADS organisations, carry out their own testing of ADS in accordance with the requirements laid down in this standard.
Annex A (Normative) References
The following normative documents contain provisions which, through reference in this text, constitute provisions of this part of the standard. For dated references, subsequent amendments to, or revisions of, any of these publications do not apply. However, parties to agreements based on this part of the standard are encouraged to investigate the possibility of applying the most recent editions of the normative documents indicated below. For undated references, the latest edition of the normative document referred to applies. Members of ISO and IEC maintain registers of currently valid ISO or EN:
The latest version/edition of these references should be used. GICHD holds copies of all references used in this standard. A register of the latest version/edition of the IMAS standards, guides and references is maintained by GICHD, and can be read on the IMAS website (www.mineactionstandards.org). National employers, mine action authorities, and other interested bodies and organisations should obtain copies before commencing mine action programmes.
-
IMAS 04.10 Glossary of mine action terms, definitions and abbreviations;
-
IMAS 07.11 Land Release
-
IMAS 07.12 Quality management in mine action;
-
IMAS 07.30 Accreditation of demining organisations;
-
IMAS 07.40 Monitoring of mine action organisations;
-
IMAS 08.20 Technical Survey
-
IMAS 09.10 Clearance Requirements
-
IMAS 09.40 Animal Detection Systems – Principles, requirements and guidelines
-
IMAS 09.41 Operational procedures for Animal Detection Systems
-
IMAS 09.44 Guide to occupational health and general dog care
Amendment record
Management of IMAS amendments
The IMAS series of standards are subject to formal review on a three-yearly basis, however this does not preclude amendments being made within these three-year periods for reasons of operational safety and efficiency or for editorial purposes.
As amendments are made to this IMAS they will be given a number, and the date and general details of the amendment shown in the table below. The amendment will also be shown on the cover page of the IMAS by the inclusion under the edition date of the phrase ‘incorporating amendment number(s) 1 etc’.
As the formal reviews of each IMAS are completed new editions may be issued. Amendments up to the date of the new edition will be incorporated into the new edition and the amendment record table cleared. Recording of amendments will then start again until a further review is carried out.
The most recently amended IMAS will be the versions that are posted on the IMAS website at www.mineactionstandards.org.
Number | Date | Amendment Details |
---|---|---|
1 |
|
Footnotes
1An empty box/panel is a test box/panel which contains no test items.